BLOG
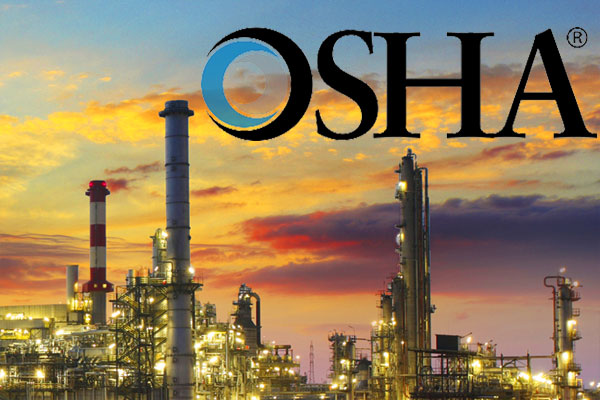
OSHA Process Safety Management
- 01 May 2018
(iii) Relief and vent systems and devices;
Pressure relief valves, rupture discs, low pressure tank vents, vacuum relief valves/vents, and other similar devices are often subject to special scrutiny by OSHA and other governmental agencies. Few other components in the petrochemical processing industry have this level of visibility or are the subject of more violations. “Relief and vent systems and devices” are specifically mentioned in several places in OSHA regulations and thus are at the top of most compliance audit checklists.
The information contained in this article includes references to OSHA publications Code of Federal Regulations 29 parts 1900 to 1910 and to OSHA 3132, and 3133.
BACKGROUND:
In 1992, OSHA (Occupation Safety and Health Administration) enacted one of the most sweeping set of regulations directly affecting processing plant safety in history. Major disasters at the Union Carbide facility in Bhopal, India (1984) that killed over 2,000 people (actually many more over time); the accident at the Phillips Refinery in Pasadena, TX (1989) that killed 23 and injured an additional 132; and the explosion at the IMC facility in Sterlington, LA (1991) that killed 8 and injured more than 128 accentuated the need for major changes. In each case, the problem was the unexpected release of toxic, reactive, or flammable chemicals that resulted in catastrophic accidents.
In 1990, Congress enacted into law, the Clean Air Act Amendments (CAAA); included were the provision that OSHA and the Environmental Protection Agency (EPA) develop a chemical process safety standard that had to include a list of highly hazardous chemicals. This required standard also included specific requirements that employers had to follow if they were manufacturing or handling chemicals on the list (more than 130 specific chemicals; reference Appendix A to 1910.119). The resulting standard, 29CFR1910.119 “Process Safety Management of Highly Hazardous Chemicals” (PSM) went into effect in 1992 with a phased implementation beginning in 1994 with final implementation required by May 26, 1997.
The fundamental basis of PSM is process hazard analysis (PHA) which is the detailed review of what can go wrong and what safeguards need to be implemented for prevention. Other key provisions include: Employee Involvement, Process Safety Information, Operating Procedures and Practices, Employee Training, Contractors, Pre-Startup Safety, Mechanical Integrity, Management of Change, Incident Investigation, Emergency Preparedness, and Compliance Audits. PSM is not a “static” process; per the regulation, “(6) At least every five (5) years after the completion of the initial process hazard analysis, the process hazard analysis shall be updated and revalidated . . .” Part of the PHA is having Process Safety Information (PSI); within the PSI are the ongoing relief system documentation requirements.
- Comment: PSM was one of the fasted promulgated regulations in history and for good reason; the protection of life and property from catastrophic releases of hazardous chemicals. It placed many challenges in front of an already complex industry; most had to start from the beginning and expend significant resources implementing the requirements of 29CFR1910.119. Record keeping, for many, had been very fragmented and often records were missing or destroyed; pressure relief engineering and maintenance records were often incomplete or non-existent. This required countless hours of re-documenting processes and equipment specifications, implementing employee training, and establishing systems to ensure continued compliance.
- While PSM is primarily directed at the petrochemical processing industry, others are targeted as well. Many plants have “PSM designated areas” that must also comply with the requirements of the standard; pulp mills with bleach plants are one notable example plus any company using chemicals listed on OSHA’s Highly Hazardous Chemical (HHC) quantity list in their processes.
PROCESS SAFETY INFORMATION:
Reference 24CFR1910.119 para. (d)
OSHA requires the compilation of written process safety information to “enable the employer and the employees involved in operating the process to identify and understand the hazards posed . . .” This information must include both hazards from the chemicals in the process and “(3) Information pertaining to the equipment in the process.” It SPECIFICALLY references “(D) relief system design and design basis;” and “(F) Design codes and standards employed;” It further says that “The employer shall document that equipment complies with recognized and generally accepted good engineering practices”.
- Comment: Key points in this portion of the standard are that the process safety information must be WRITTEN and that specific pieces of equipment MUST be included. Relief systems would include all types of overpressure protection as well as vacuum protection. The specific method used for the sizing and selection of each device must be documented along with the codes and standards used. Additionally, the regulation requires RAGAGEP (the use of recognized (e.g. ASME, API, etc.) and generally accepted good engineering practices).
- The challenge for many users is that plants often had fragmented or, in many cases, no real record keeping system; design reports were misplaced or discarded and many devices were literally sized and selected “on the back of an envelope”. This was especially true for smaller producers; many dollars were spent with outside engineering firms verifying the adequacy of the design of their pressure/vacuum relief systems. Note: System refers not only to the device, but also to the piping, equipment, and instrumentation surrounding the device. Inlet pressure losses need to be below that specified by API 520 and discharge piping also needs special attention, especially if it is connected to a manifold that directs the flow to a scrubber or flare.
- The requirement to maintain these records can easily be solved by sophisticated asset management software such as GE’s ValvKeep®. Typical asset management software only provides a method for collecting information in a spreadsheet format and then providing maintenance repair reports. ValvKeep® efficiently keeps track of sizing/selection documents, P&ID’s, process information, protected equipment information, installation images, and inspection/repair documentation.
Generally accepted engineering practices (plus others):
MECHANICAL INTEGRITY:
Reference 29CFR1910.119 para. (d)
This section of the standard specifically applies (per OSHA) to “ (i) Pressure vessels and storage tank; (ii) Piping systems (including piping components such as valves); (iii) Relief and vent systems and devices; (iv) Emergency shutdown systems; Controls (including monitoring devices and sensors, alarms, and interlocks) and, (vi) pumps.” The practice of running equipment to failure is no longer permissible and employers must review their maintenance programs and PM schedules to see if there are areas where this practice can be replaced with “an on-going mechanical integrity program”.
OSHA requires that equipment used to process, store, or handle highly hazardous chemicals has to be designed, constructed, installed, and MAINTAINED to minimize the risk of releases. Elements of the program must include: identifying and categorizing equipment and instrumentation; inspections, tests and their frequency; maintenance procedures; training of maintenance personnel; criteria for acceptable test results; documentation of test and inspection results; and documentation of manufacturer recommendations for equipment and instrumentation. The employer should set priorities for which pieces of equipment require closer scrutiny than others. (Reference OSHA publication 3133)
A key component of this section is (4) Inspection and testing. OSHA states that “(4) (ii) Inspection and testing procedures shall follow recognized and generally accepted good engineering practices. (iii) The frequency of inspection and tests of process equipment shall be consistent with applicable manufacturer’s recommendations and good engineering practices and more frequently if determined to be necessary by prior operating experience. (iv) The employer shall document each inspection and test that has been performed on process equipment.”
Comment: The KEY point in this section is that employers must embrace PREVENTATIVE maintenance as a major component of mechanical integrity. Valves, Relief Valves (and associated piping), Controls, and Pumps are all SPECIFICALLY identified as being key pieces of process equipment covered by this standard. An additional point is the phrase in (j)(2) Written Procedures; . . . “to maintain the ON-GOING integrity of process equipment.” The mechanical integrity paragraphs in the standard are not meant to be a single EVENT but an evergreen PROCESS.
OSHA is adamant about the continuity of the processes/procedures that employers put into place to ensure the safety of their operations that are subject to this standard. The requirement to thoroughly document the design basis for identified process equipment was previously discussed under PROCESS SAFETY INFORMATION. OSHA then requires assurance that the equipment was “installed properly and consistent with design specifications and the MANUFACTURER’S INSTRUCTIONS.” It is important that employers KNOW what these instructions are and that they maintain documentation showing compliance. Utilizing the Original equipment Manufacturer (OEM) to assist in the installation and commissioning of the equipment provides an additional level of Mechanical Integrity compliance.
Once operations commence, OSHA is very specific about the requirements for INSPECTION AND TESTING; again, they describe a PROCESS rather than a single EVENT. So, how often should an employer address this issue on identified pieces of key process equipment? The standard says, “(iii) The frequency of inspections and tests shall be consistent with applicable manufacturer’s recommendations and good engineering practices, and more frequently if determined to be necessary by prior operating experience.” This puts the burden squarely on the employer since most OEM’s only “suggest”, but seldom “recommend” due to the wide variety of possible applications. Additionally, what does “prior operating experience” truly mean and how is this realistically determined?
A couple of other important points are that testing and inspection should follow procedures that are in accordance with recognized and generally accepted good engineering practices (see para. d above). Also, the employer must DOCUMENT each inspection and test that has been performed. The first point is fairly straightforward in the Americas since the ASME, API, and NBIC are all universally recognized standards and are certainly considered “good engineering practices”. The National Board VR program for the inspection, repair, and testing of pressure relief devices has actually been written into law in most states as has the ASME Code for pressure vessels; for other key pieces of equipment API standards are the most widely recognized. In each standard, a cornerstone of their quality systems is documentation and traceability.
Many employers find these directives daunting; there is much work required with increasingly diminishing resources. Often the solution is outsourcing many of these tasks to the OEM or organizations that specialize in the inspection, testing, and when required, repair of the process equipment specified in the standard. Many OEM’s have authorized highly skilled service organizations to fulfill this need on their behalf. These factory authorized service centers typically have undergone a very thorough selection process and are required to have highly trained and certified technicians that work under a very stringent QC program. OEM’s provide proprietary engineering and maintenance procedures for their use and insist that only OEM replacement parts be used in repairs.
FINAL THOUGHTS:
GE’s Green Tag Center (GTC) program for Consolidated® pressure relief valves was established in 1982 and is considered to be one of the very best in the industry. GTC’s undergo a rigorous selection process and are audited ANNUALLY to ensure continued excellence. Each GTC is certified by both the American Society of Mechanical Engineers (ASME) for the assemble of NEW pressure relief valves and the National Board of Boiler and Pressure Vessel Inspectors (NBBI) for the REPAIR of pressure relief valves under their VR program. Each technician is factory trained and certified at multiple levels and must be RECERTIFED each year. GTC’s have access to the most recent engineering standards, procedures, and techniques to insure that each valve that leaves their facility or is serviced at a customer’s plant site meets all OEM requirements. Only new OEM parts are used in GTC centers and their reputation for integrity is unsurpassed.
Documentation is what sets GTC’s apart from other OEM service companies. Utilizing the proprietary ValvKeep® (VK) asset management software makes OSHA PSM compliance much less onerous. Actually, VK was originally developed with OSHA compliance in mind. GTC’s utilizing VK offer customers immediate access to all information related to a variety of process equipment including Pressure Relief Valves & Vents, Control Valves & Associated equipment, Motor Operated Valves, and Manual Line Valves. Design and selection (PSV sizing scenarios), P&ID’s, Process information, and Images are all captured and stored for immediate retrieval along with all historical maintenance records. All of this documentation is required by OSHA.
ValvKeep® also handles the OSHA requirement to establish maintenance intervals “based on prior operating experience” by providing a variety of analysis functions that allow customers to best determine the appropriate maintenance cycle. Once determined, VK automatically tracks each piece of equipment and proactively notifies the customer when the next required maintenance date is approaching. OSHA “Mechanical Integrity” compliance is NO PROBLEM with ValvKeep®.