BLOG
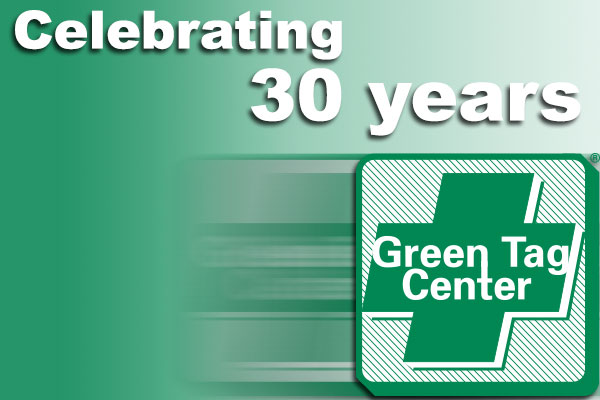
Green Tag Network – Celebrating 30 years
- 06 May 2014
From the very beginning when Consolidated pressure relief valves were first manufactured by Ashcroft Manufacturing Co., they became and industry leader. Throughout their 130-year evolution – through Manning, Maxwell, & Moore; Dresser Industries; Halliburton; Dresser Inc; and now GE- they have led the way in the pressure relief valve industry.
Initially a large number of companies distributed Consolidated pressure relief valves, pressure gauges, pipe fittings, duct tape, and other mill supply products across the United States.
There was also a network of assemblers-only a few at first-who assembled and tested new Consolidated pressure relief valves from component parts as authorized by the manufacturer and ASME. They also repaired pressure relief valves, but without approval or authorization from the manufacturer – who was also in the repair business and was the only “Factory-Authorized” source for pressure relief valve repair.
Over time the need for distributors diminished, and they were gradually dropped until only a few remained.30 Years of innovation…..Building on the Legacy
Responding to the need to validate fragmented rules and regulations in place in many states, the National Board of Boiler & Pressure Vessels (NBBI) launched a VR Repair Authorization program in 1976 – providing certificates of authorization to organizations that met their valve repair requirements. Many assemblers embraced this new program and voluntarily became VR Certified.
In 1981, when Ted Myers became president of the former Dresser Inc., he began to question the status quo. His vision encompassed a better way to promote the Consolidated pressure relief valves and replacement parts, along with a way for the former Dresser company to participate in the repair revenue being generated by it’s Assemblers.
The vision became reality in 1982 when the Green Tag Program was launched, adapting the “Green Cross” phrase current at the time, which was often equated with safety. The term “Green Cross for Safety” still has meaning today.
All assemblers authorized by the former Dresser company were invited to become part of the new Green Tag Center (GTC) program – which embraced the successful assembler program for new pressure relief valves while adding the concept of factory-authorized repair. This additional concept was to be funded by a “franchise fee” tied to the volume of repair performed by the assembler – turned – GTC. In exchange for this fee, Green Tag Centers were provided with factory training, proprietary repair instructions, and proprietary engineering information in the form of critical dimensions for specific parts. They were also subject to factory audits.
This dramatic departure from the status quo caused some consternation among those in the assembler network who felt the manufacturer had intruded into an arena exclusive to the assemblers (i.e. repair). few assemblers entirely rejected the idea of becoming a GTC. However, after considerable discussion, most assemblers agreed that Mr. Meyers had indeed developed the framework for an industry-altering program, and the GTC concept became a reality. The slogan “We build safety into every valve and then help you keep it” became the mantra of the GTC program.
No other program could match the comprehensive nature of the one launched by Mr. Meyers, and key industry players hailed it as a great success. Unfortunately, Mr. Myers died before seeing the program fully implemented, but his vision quickly spread across the industry.
When the need for a factory-authorized test device was identified, the Electronic Valve Tester (EVT) was born. While the basic technology wasn’t new, the concept of a manufacture-developed test device was. Coupled with the GTC program, the EVT was an instant success further strengthening the reputation of the GTC initiative.
The true strength of the GTC program demonstrated by the unity and camaraderie of the GTCs themselves. Although management could change at any given manufacturer, the continuity of the program was preserved by the individual GTCs who continued to experience success with the program. Over the years, the franchise fee was eliminated, and the program evolved into what it is today.
While other manufacturers tried to initiate similar programs, they often had little more to offer than a catchy name and a limited capacity far removed from the thriving GTC program. Innovation continues to drive the Green Tag Center program, and GTCs have formalized their ability to share inventory and information via the GTC Net. These days, more than $35 million in shared inventory is available at a moment’s notice.
In 1992, when OSHA promulgated the Process Safety Management provision, GTCs were well prepared with the asset management concept they had developed. Today, the ValvKeep valve management software suite is an industry leader that continues to distinguish GTCs from their competitors.
Visionary ideas were the foundation of the GTC program, and they continue to drive our commitment to excellence. New valve products are being developed and new marketing tools are quickly embraced. Each new generation of management, both at GTCs and at the manufacturer, continue to build on one of the strongest legacies in the industry. Thirty years after its conception, the Green Tag Center program still is an industry leader in the pressure relief valve industry.Today, GE’s Green Tag Center Network Consist of More Than 80 Facilities, Located in More Than 30 Countries Worldwide.